Strong partner at your side
Solid in preparation, precise in implementation.
Hatz Components appears as a strong partner right from the start. Lean structures and the company’s sustainability-oriented philosophy promise high-precision products for demanding applications.
01.
Verification
According to your requirements, our experienced engineers will support you to enable the best possible manufacturability of your project.
02.
Prototyping
Using the latest software and machines, we create the prototype for you.
03.
Serialization
This is where performance comes from. In detailed precision work, we develop your product from the prototype to series maturity. In a stable process, we ensure 100,000-fold replication with the highest quality at the same time, and we are constantly optimizing the processing of the connecting rod.
04.
Series
We continuously monitor all processes for you, evaluate and fine-tune the connecting rod. The goal: to forge the perfect connecting rod for you from the original requirement verification.
05.
Administration
We can keep you up to date – during production and afterwards, in order to ensure that your project is successful in the long term.
04.
Series
We continuously monitor all processes for you, evaluate and fine-tune the connecting rod. The goal: to forge the perfect connecting rod for you from the original requirement verification.
05.
Administration
We can keep you up to date – during production and afterwards, in order to ensure that your project is successful in the long term.
If you have any questions or need support, please contact us on: +49 8531 9781 100
Performance connecting rods
Success is in the details
Hatz Components is your quality provider in the development and production of connecting rods. State-of-the-art technologies enable us to guide your project flexibly and precisely into and through production.
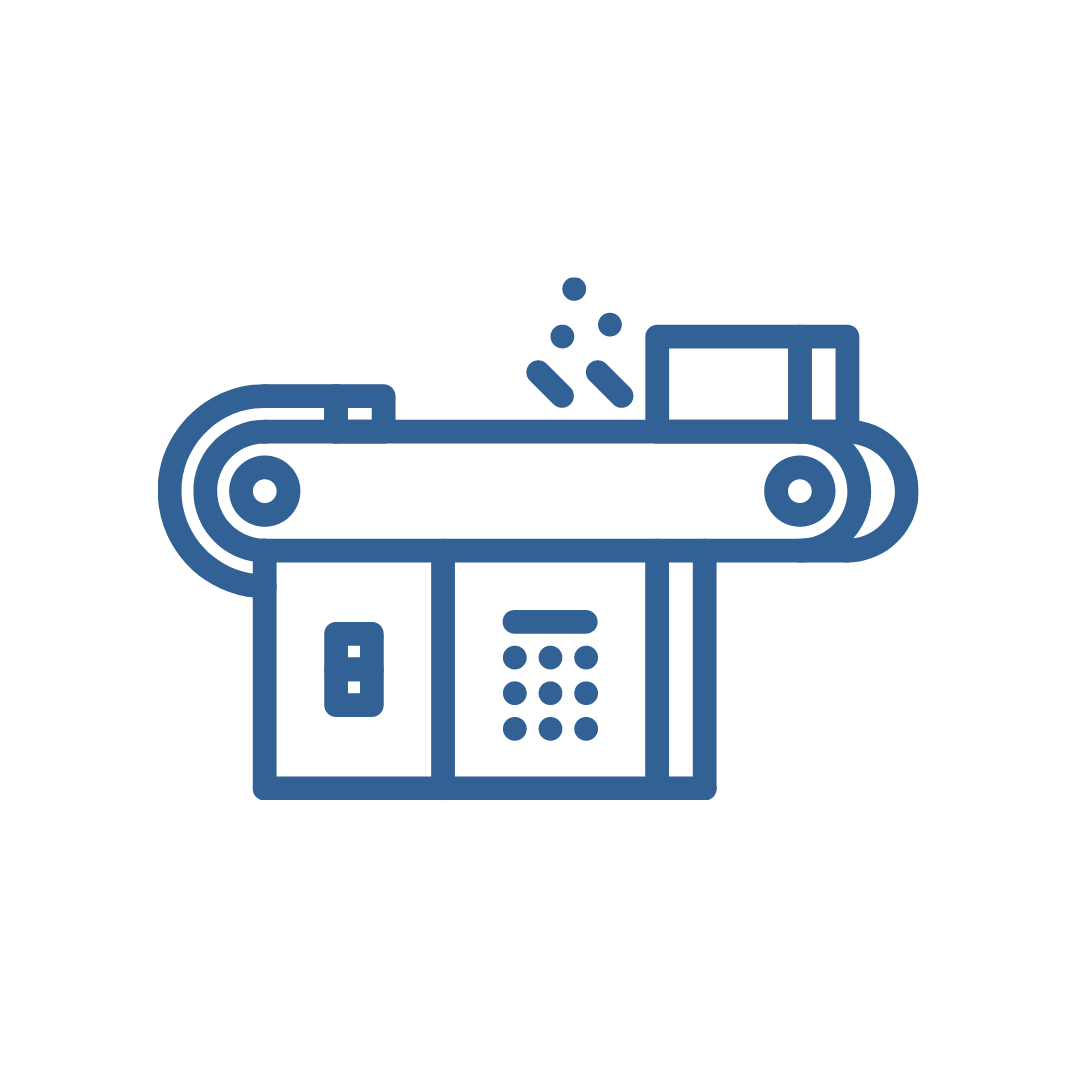
Grinding and Milling
The basic requirement for our high-performance connecting rods is the high-quality industrial machine park consisting of high-tech grinding and milling machines. In the first step, the forging die (blank) is pre-ground or pre-milled. Both in the prototype and in the later series – in the prototype regardless of whether it is made of “solid” metal block or a forged blank. This means that the most efficient machining solution can be implemented for each type of connecting rod.
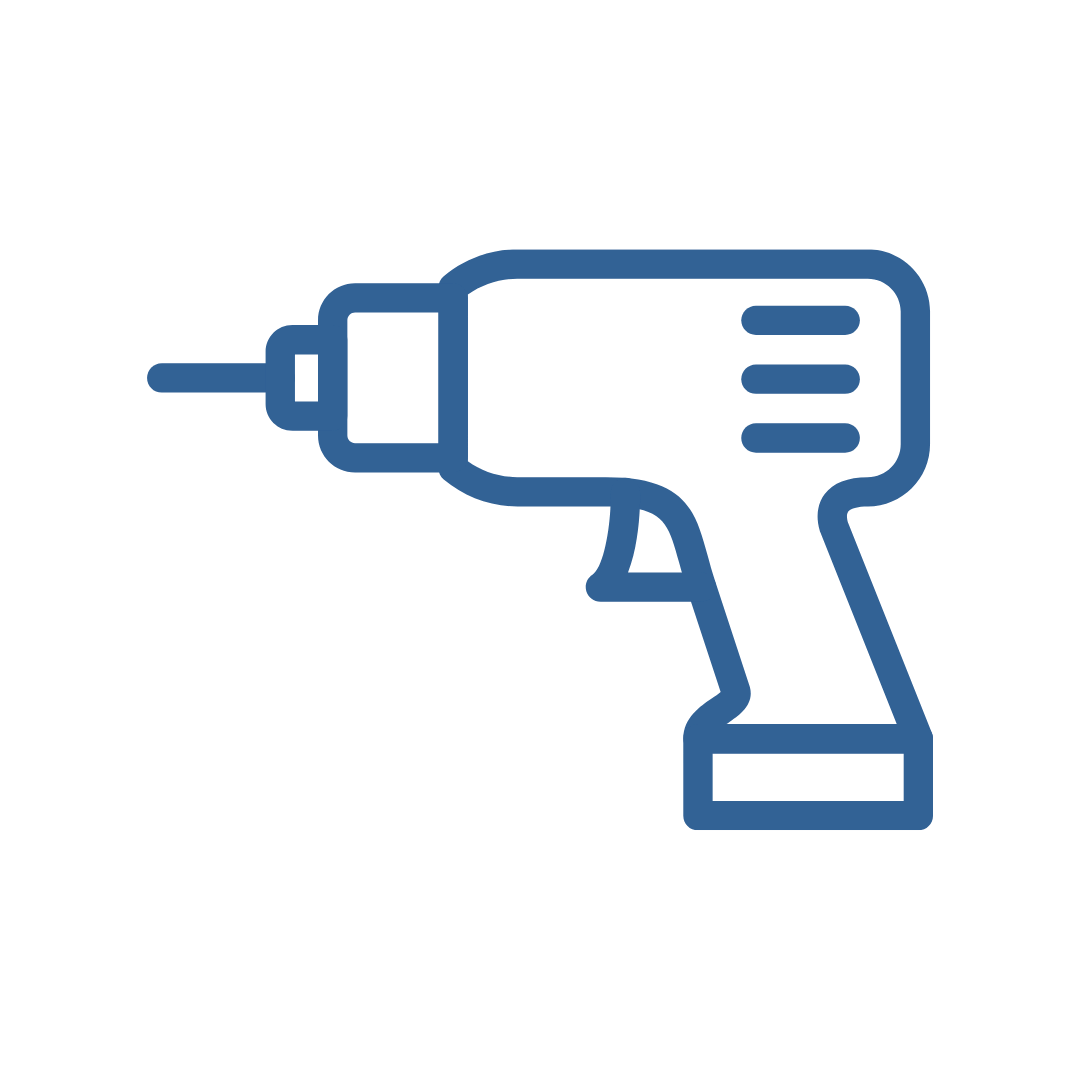
Drill
In order to withstand the stresses in the engine, the connecting rods must have the highest bending, torsional and wear resistance as the basis for their use. In elaborate pre-processing for the later laser cracking, the connecting rod eyes are first pre-processed, reamed or spindled, depending on the customer’s requirements. This also with a special surface quality for the optimal press fit of the plain bearing. The processing of the individual screw supports, screw holes and threads, which can not only be cut in the classic way, but also shaped or milled, follows this.
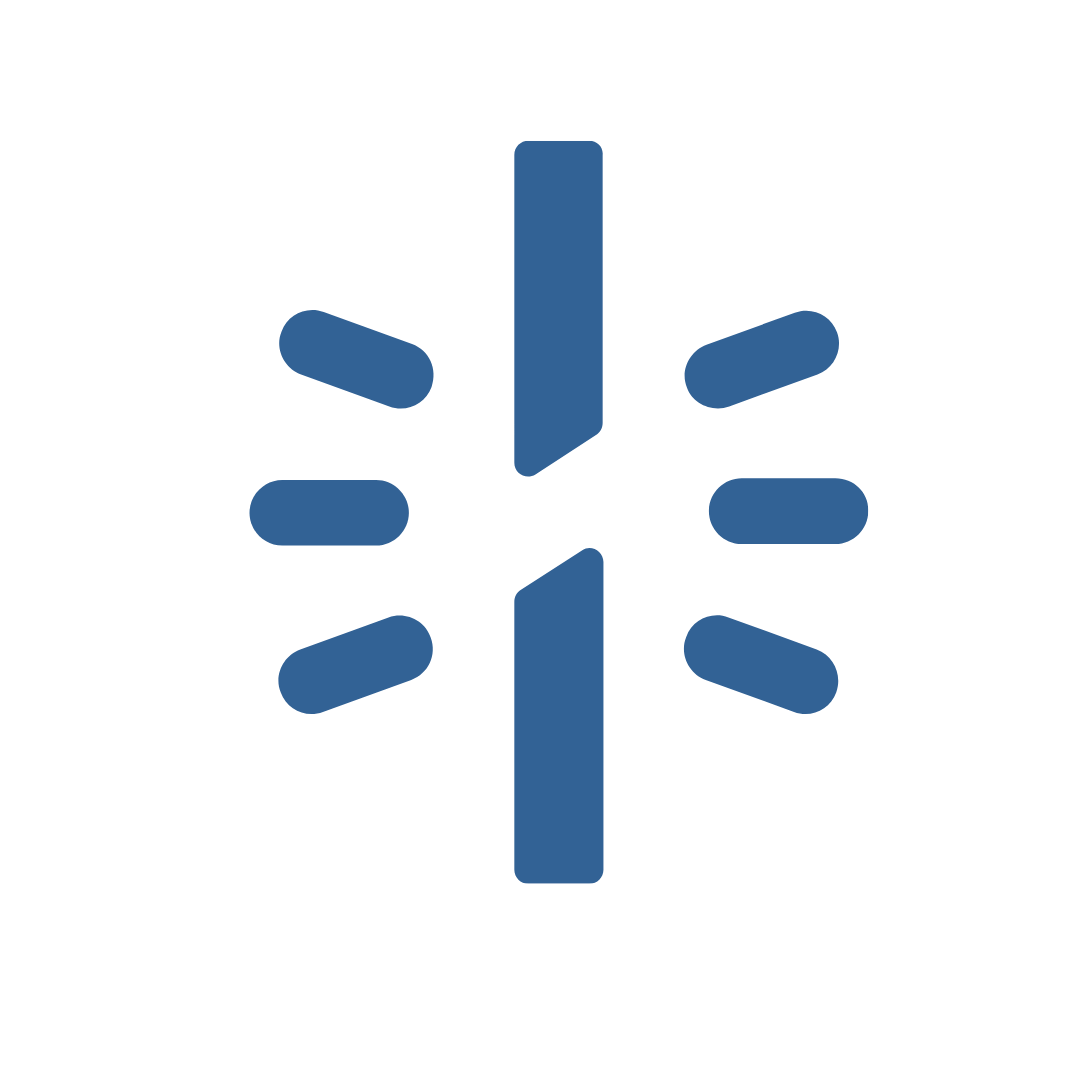
Laser Cracking Technology
Our claim is superior process reliability and this is exactly where we make the difference: An optimal cracking result is achieved on self-developed machines and the use of special cracking shells. In contrast to expensive supercooling, we prevent inhomogeneous crack surfaces with the help of our own sophisticated and experienced technology. By constantly optimizing all devices, we always achieve a lean, efficient and more precise process.
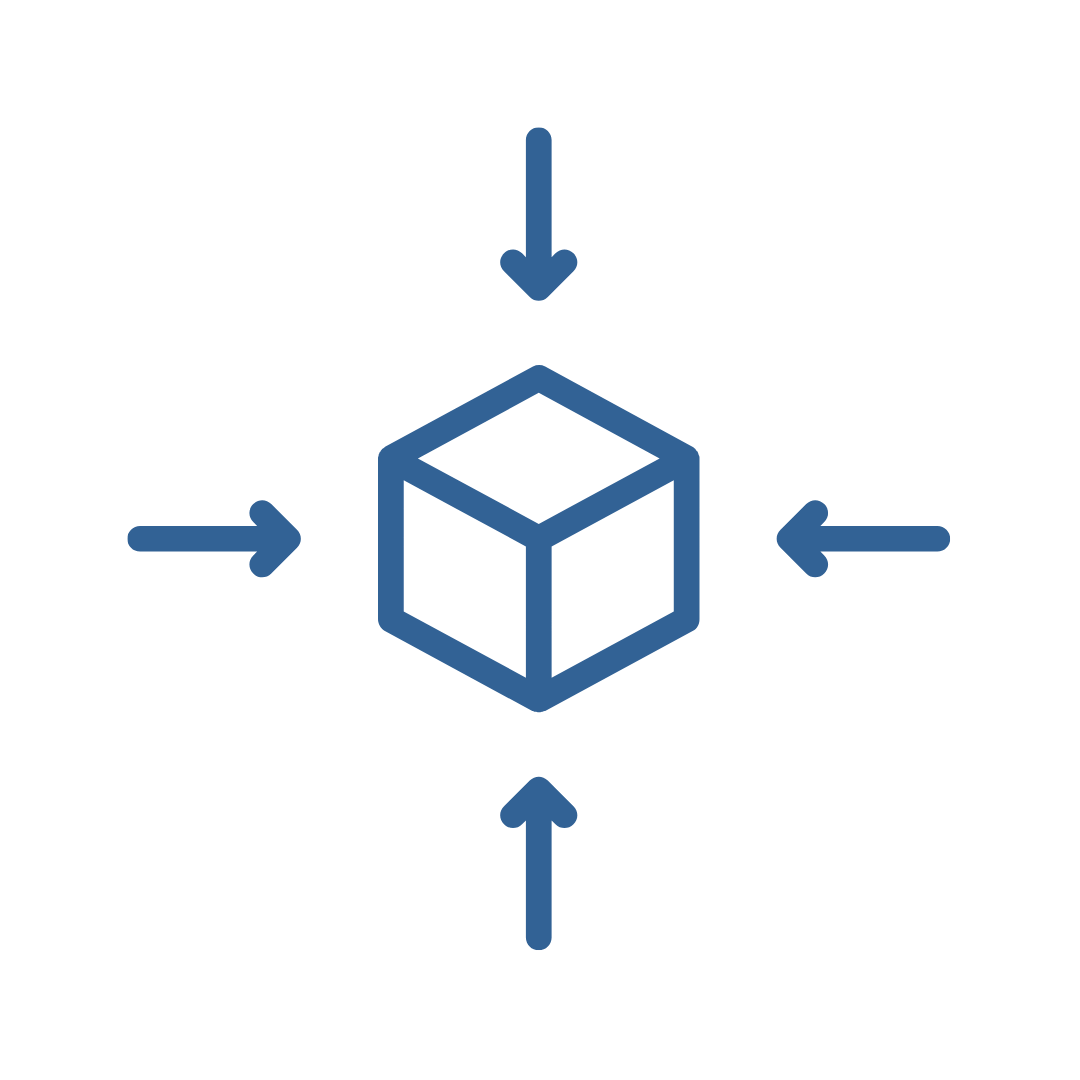
Calibrating and Finishing
In order for the engine to be used as an overall construction and engineering masterpiece with low wear and maximum efficiency, the pressed bushing in the small connecting rod eye is calibrated in the process, materials are adjusted if necessary, for example to optimize sliding properties, and both eyes are finely ground. Minimal deformations are removed. The trapezoids on the small eye are also lowered. Before the large eye is finely machined, the retaining grooves are attached and the installation safety device for the charging cradle is set, the screws on the connecting rod are loosened and screwed on again, thus compensating for tension in the material.
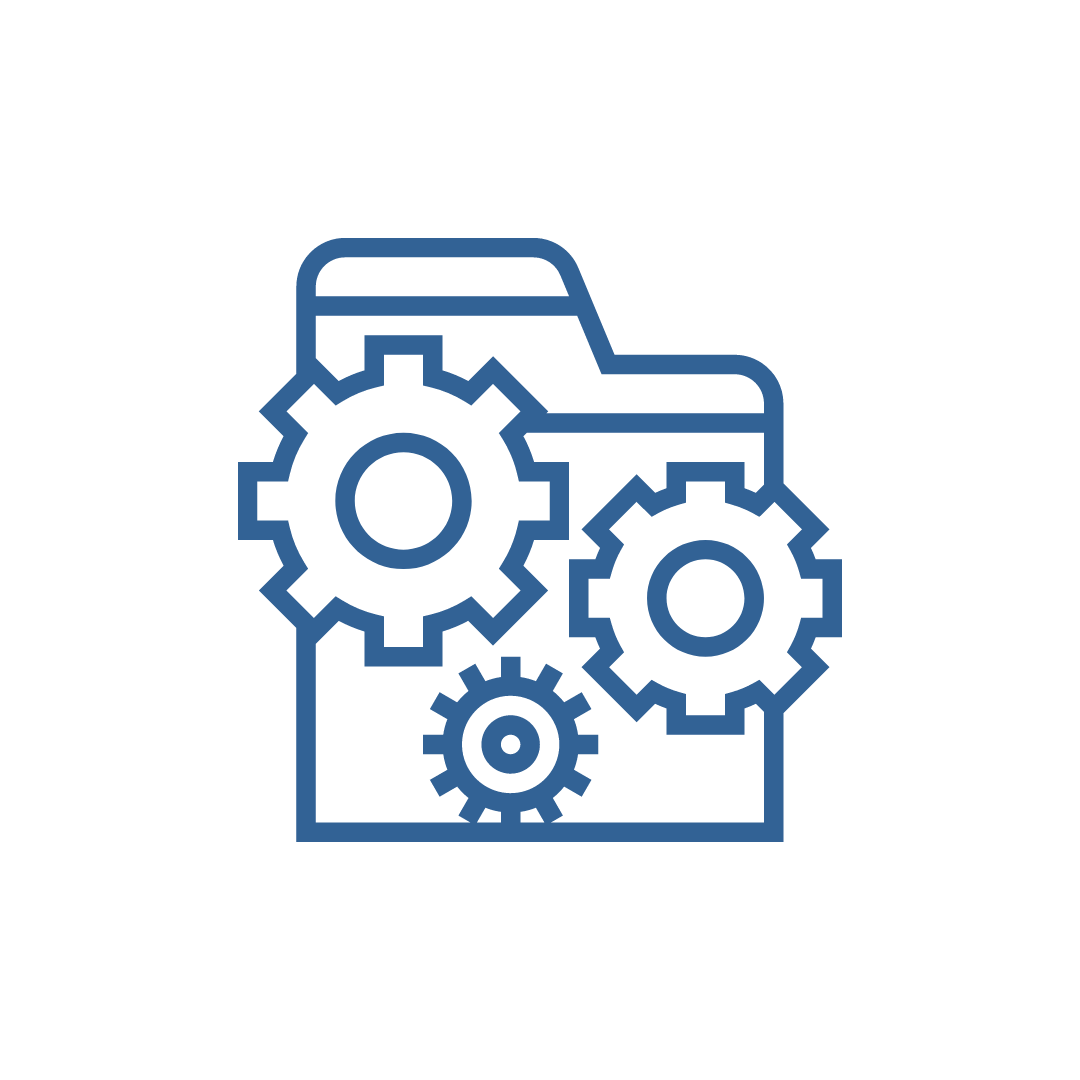
Post production and Machining
Before the finished connecting rod is ready for dispatch to the customer, the large eye is finally fine-turned to ensure the required roundness. Depending on our customers’ wishes, there is also the option of a shaped or oval bore for the small eye. In addition to the specially developed laser crack technology, this is another great advantage of Hatz Components, which contains a great deal of knowledge and experience: the lubrication is improved to the maximum and signs of wear are minimized. After applying special honing structures to the connecting rod, the weight of the connecting rod eyes is carefully checked and the total weight is determined according to the drawing specifications. Before the decisive last step, the main features of the connecting rod are measured with the utmost precision. These include diameter, center distance, torsion, and many more.
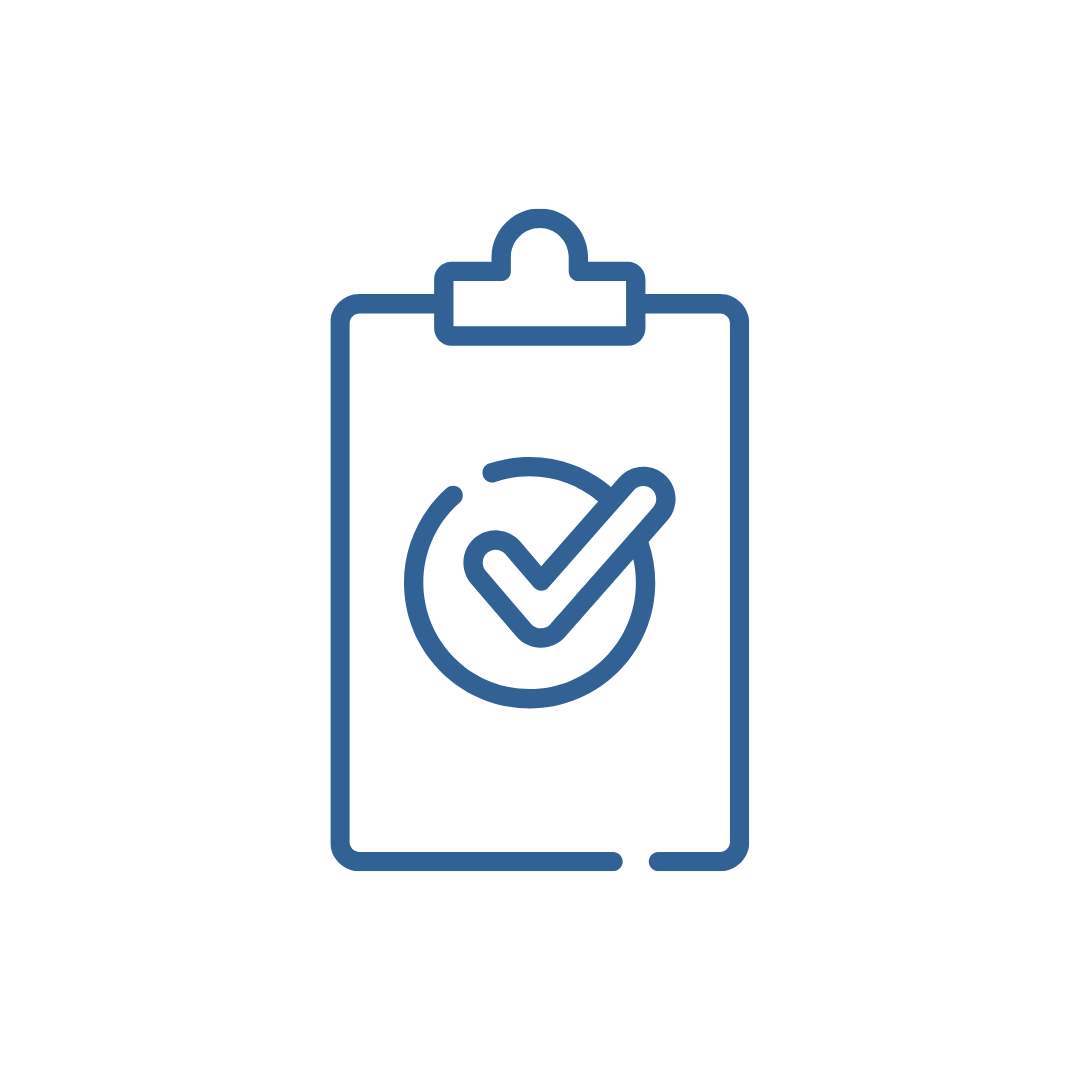
Finishing and Quality Control
On the home straight of the production process, there is a 100 percent inspection of the connecting rods under the highest standards of cleanliness and the best lighting conditions. This means that every single component, every connecting rod, is subjected to a final visual inspection. The quality is determined and checked to see whether all processing steps that have been completed meet the high requirements of Hatz Components. In the last step, Hatz Components prepares the finished connecting rod individually and tailored to the following production processes for shipping and you will receive your connecting rod delivery with our initial sample documents.